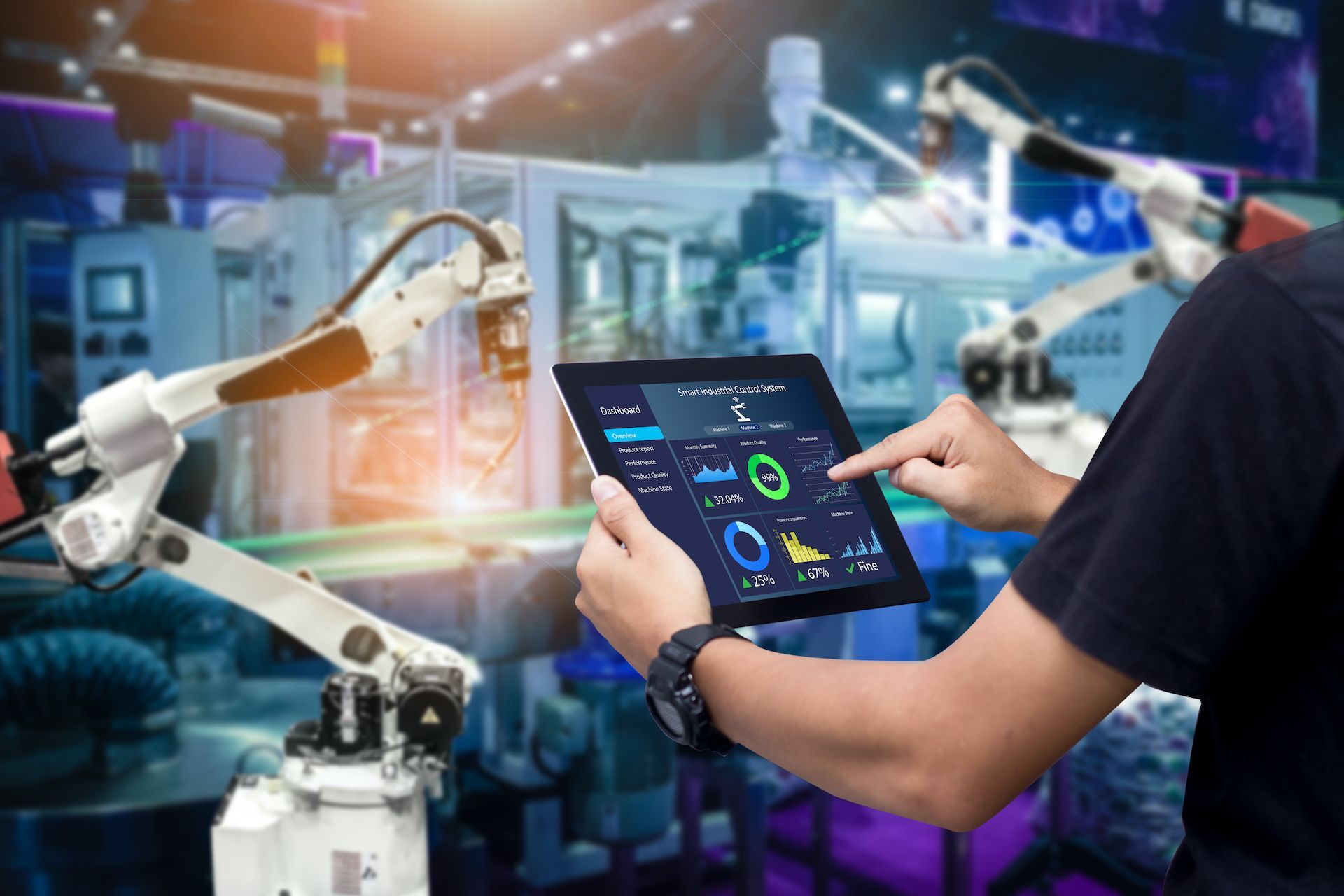
βοΈ How connected sensors revolutionize industrial and hydraulic systems
The Internet of Things, or IoT, is now taking the heavy industry by storm. Connected sensors make everything from mechanical to hydraulic systems smarter and more efficient.
Share this story!
The industry variant of the IoT, or the Internet of Things, has its own abbreviation, IIoT. But it's basically the same thing. There is a large amount of connected sensors and other digital devices that send and receive information via the Internet. The information can be processed and analyzed and provide lots of benefits.
The difference is possibly that even higher quality requirements are set within IIoT. This high-quality variant of IoT affects all sectors of the heavy industry, including hydraulic power.
Hydraulic , or fluid-based, power is found in many applications and is critical to many industries but is, for most people, unknown. One example you probably see quite regularly are cranes and excavators where hydraulics are used to operate the crane with tremendous power and precision.
This is a good example because hydraulics are used when the demands on power are high, for example in mobile machines or equipment in heavy industry. The technology is based on the fact that force and movement are achieved by means of compressed fluids. Basically, a hydraulic system is based on a pump that creates pressure and flow, a valve that regulates pressure and direction of the fluid, and a cylinder or motor that creates a movement.
Many conventional hydraulic power systems integrate digital components and generate a large amount of operational data. However, much of this information is not available, which limits its use. New technology blurs the line between the valve or actuator, which regulates the fluid, and the sensor in a hydraulic system. This enables new features and increases efficiency.
βοΈ Warp News is run by a non-profit foundation. Would you like to support our efforts to spread fact-based optimism and gain access to more of what we do? Read more about becoming a WIP member!
Better use of data
Conventional solenoid valves, electromagnetically controlled valves that control the flow of a fluid in a hydraulic system, are controlled by simple control units, but more advanced technology has been introduced in recent years. It is now normal for the systems that control a solenoid valve to include built-in diagnostic sensors that keep track of operating variables such as temperature, flow and voltage.
These sensors collect and process significant amounts of data, but are rarely used effectively. The information is used to control the valve but is not integrated with other systems. IoT sensors and actuators, on the other hand, can collect this data and communicate with local construction systems and transmit this data over the Internet where it can be processed and used to create new insights and benefits.
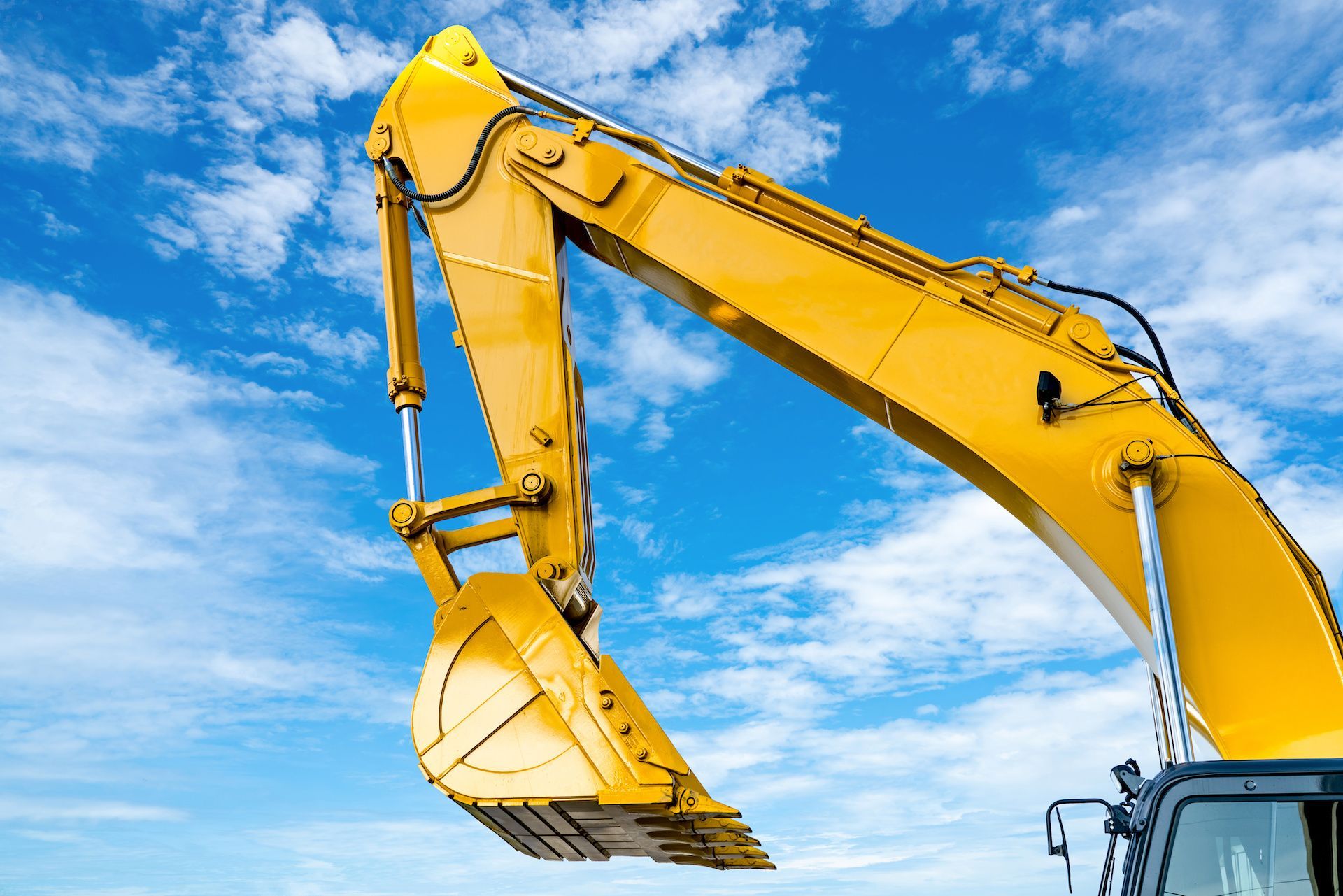
IIoT vitamin injection for hydraulic systems
IIoT controllers in hydraulic power systems provide many of the advantages we see in other industrial applications. Remote control of plant systems is one of the biggest advantages of the technology. Some IoT units designed for hydraulic systems consolidate the actuator, the motor that opens or closes the solenoid valve, and the sensor into a single unit. With an IoT solenoid valve installed, it is possible to handle the system, a worker can handle it without direct access to the valve itself. Often, even a workstation does not need to be in place. Many IoT actuators can be operated via a smartphone or laptop.
Remote access to system data can provide other benefits. All hydraulic power systems can benefit from regular fluid control, monitoring wear and tear and other problems. Over time, if this type of inspection is neglected, simple problems can lead to serious damage or equipment failure. Often, small and medium-sized plants have no technician or engineer in place who can troubleshoot complex problems. If a system starts to malfunction, the plant manager must contact a service company or supplier and request a technician who can inspect the system.
With the right IoT device in place, the plant can instead send operating data directly from the hydraulic system to the service company that may be able to solve or identify the problem without sending a technician.
IIoT creates predictability
IoT sensors also enable plant managers to use predictable maintenance strategies. A sensor in the right place can detect vibrations that may indicate upcoming faults or suboptimal flow settings.
Gas leaks in fluid power systems that rely on compressed gas can be costly, reduce machine efficiency and create serious safety risks. Ultrasonic IIoT sensors can be used to detect gas leaks and some companies already sell IoT sensors designed to do this.
When the predictive maintenance system detects unsafe or sub-optimal operating conditions, it can notify employees that maintenance is needed. Some systems that have direct control over the actuators may also be able to adjust the flow or switch off the system if necessary.
What are the risks with hydraulics and IIoT?
IIoT systems used for hydraulic systems will face similar challenges to all other industrial IoT applications.
For many, security is a significant problem. As with IoT devices for the consumer market, industrial sensors, actuators and valves can provide an attack vector for hackers or cyber criminals who want control over the facility's network. While conventional solenoid valves are usually air-tapped and controlled by a system that may not be connected to the Internet, connected IoT devices may be more vulnerable.
Limited connection can also be a challenge, especially in rural areas. A solid internet connection is not a given and 4G networks are sometimes not enough to handle a large number of devices connecting to the same cell tower. 5G is therefore very interesting as it can deal with these problems. The next generation of mobile technology, which already exists in some places in the country, has technology like massive MIMO which improves the ability of individual cell towers to handle many devices.
In summary, the benefits are enormous, while the disadvantages of introducing IIoT in hydraulic systems are manageable. It will enable remote monitoring and control of systems and pave the way for advanced predictable maintenance strategies. For plants that can integrate this technology into their systems, a revolution awaits.
How does hydraulics work?
Hydraulics is a word that comes from the Greek hydor, "water" and aulo's, "pipe".
Today, hydraulics is used as a collective term for components that are part of a hydraulic system. Hydraulics is, in short, a smart way of transferring, storing and controlling energy with the help of fluid and has many applications in engineering. Modern hydraulics have revolutionized industry and the way it works, but also how machines and vehicles work.